When diving into a construction project, it’s imperative to understand that only some team members are seasoned builders or craftsmen. Some might be handling procurement or administrative duties and may not be well-versed in the nuanced terminologies of the plywood manufacturing sphere.
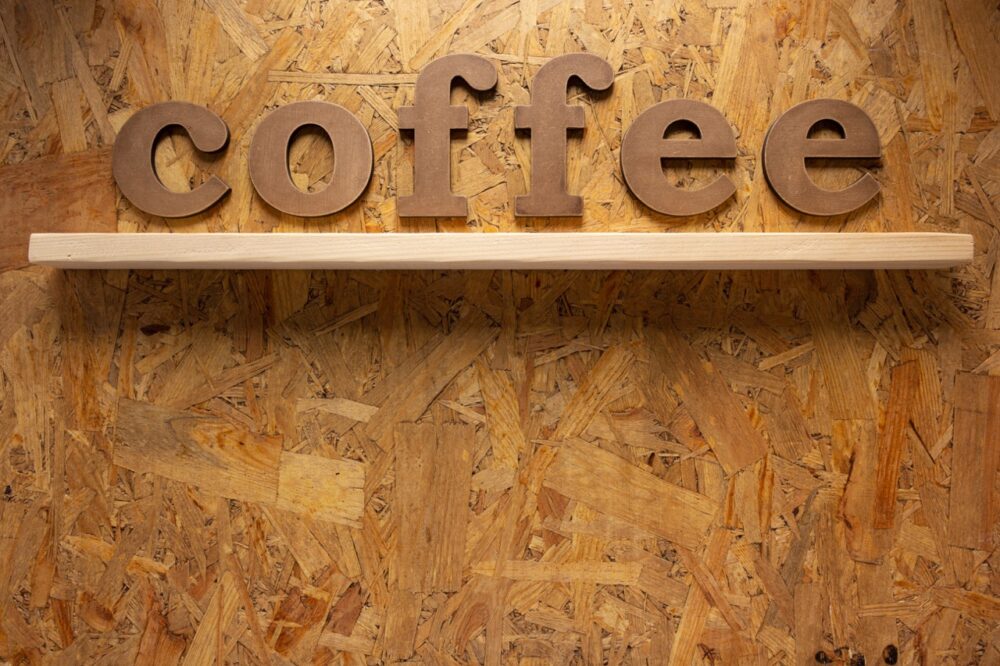
This knowledge gap could lead to misunderstandings with your plywood supplier and result in time-consuming blunders or incorrect material choices. Therefore, we’ve curated a list of vital plywood terminologies that everyone should acquaint themselves with:
Vocabulary Breakdown:
- Back: Refers to the side of the plywood sheets with a lower-grade outer veneer. A clear distinction between the front and back can often be observed in decorative plywood varieties, such as the 9mm plywood.
- Cathedral Grain: Recognizable by a sequence of aligned “V” and upside-down “V” patterns, this term defines a particular grain layout visible in plain-sliced or flat-cut veneers.
- Core: The inner layers of a completed plywood sheet, the core can be composed of various materials based on the plywood type. This includes options like lumber, veneers, particleboard, MDF, or even a blend of these materials. Notably, the grain of the core always runs perpendicular to the exterior layers of the plywood.
- Crossbar: An imperfection in the wood grain that extends at right angles to the board’s length. Premium quality plywood typically contains minimal such defects, while the more budget-friendly options may have them.
- Cut: Defines how a log gets sliced. There are various methods like rotary cut, rift cut, plain slice, quarter slice, and half-round slice.
- Delamination: This represents an undesired separation between the layers of a plywood sheet, generally caused by inferior adhesive bonding.
- Equilibrium Moisture Content (EMC): Refers to the moisture level a wood-based component (including solid wood, plywood, MDF, particleboard, or chipboard) needs to maintain. Exceeding or falling short of this level recurrently may lead to the material warping or incurring significant damage.
- Face: Often termed as the “front,” this is the side of the plywood sheet with a superior grade.
- Grade: A classification system used for veneers based on their quality and species. The front side has 6 standard grades ranging from AA to E, while the back has grades numbered 1 through 4.
- Grain: Defines the inherent pattern and direction of growth observed in the wood fibers present in a veneer.
- Half-Round Slicing: A cutting technique wherein a log is sliced tangentially to its growth rings, yielding either a plain sliced or rotary grain pattern.
- Hardwood: Refers to wood derived from deciduous tree species like maple, ash, and oak. It’s crucial not to equate this term with the wood’s actual hardness or density.
- Rotary Cut: A cutting technique where a log is peeled to produce a veneer, leading to a distinct wild grain appearance. The entire log rotates against a stationary blade during this process.
- Sapwood: Represents the living layers of wood in lumber. These layers are positioned between a living tree’s core wood and bark, playing a crucial role in nutrient storage and transport.
- Slip-Matching: A technique wherein veneers are placed adjacent to each other, ensuring a consistent grain pattern on the final product.
- Splits: Cracks appearing in the wood fibers of a veneer, extending parallel to the grain direction.
- Sonapanel: An innovative acoustic plywood solution. This system effectively tackles ambient noise, minimizing sound reflection. Its applications are vast, ranging from conference rooms and reception areas to large lecture halls and personal home theatres.