In the dynamic sphere of manufacturing and supply chain management, efficiency, and agility are pivotal to success. Among the various tools and strategies available to industry professionals, the kanban inventory system stands out as an instrumental approach to managing production workflows and inventory levels. Characterized by its visual nature and just-in-time philosophy, kanban can drive significant improvements in operations and customer satisfaction. In this article, we delve into the core benefits of integrating a kanban system into your manufacturing and supply process. Below, discover how your business can transform through this refined method.
Understanding Kanban Inventory System in Modern Manufacturing
The kanban inventory system, a concept that originated in Japan, is a methodical approach designed to enhance manufacturing processes. At its heart is an intuitive visual system that uses cards or signals to represent work items and inventory levels. This simplicity in design belies its profound impact on production lines, allowing for real-time updates and responses to demand fluctuations.
In modern manufacturing, kanban facilitates a clear understanding of workflow and resource allocation. It helps eliminate overproduction, one of the principal wastes in the lean manufacturing framework. The system’s flexibility allows it to be tailored to various operational scales, whether in sprawling factories or smaller workshops.
Integration of technology has further refined the kanban inventory system. Digital kanban boards and analytics tools have made monitoring production cycles and predicting demand more accurate than ever before. This digitization aligns well with Industry 4.0 principles, leveraging data to optimize manufacturing processes.
Improving Production Flow and Efficiency Wh Kanban
The implementation of kanban inherently promotes the streamlining of production flow. Its pull system ensures that components and products are produced only as needed, thereby minimizing the risk of overstocking and underutilization of resources. This approach ensures a more efficient workflow and better allocation of personnel and materials.
Kanban’s visual nature is key to improving process clarity among team members. By providing an at-a-glance view of the production pipeline, employees can quickly identify which tasks require immediate attention or replenishment. This enhances overall efficiency and reduces the potential for bottlenecks.
For instance, when a kanban card signals a low inventory level, teams can swiftly adjust without needing micromanagement or excessive administration. This responsiveness not only saves time but also empowers staff to act decisively, fostering a more dynamic and engaged workforce.
Inventory Reduction and Cost Savings: The Kanban Effect
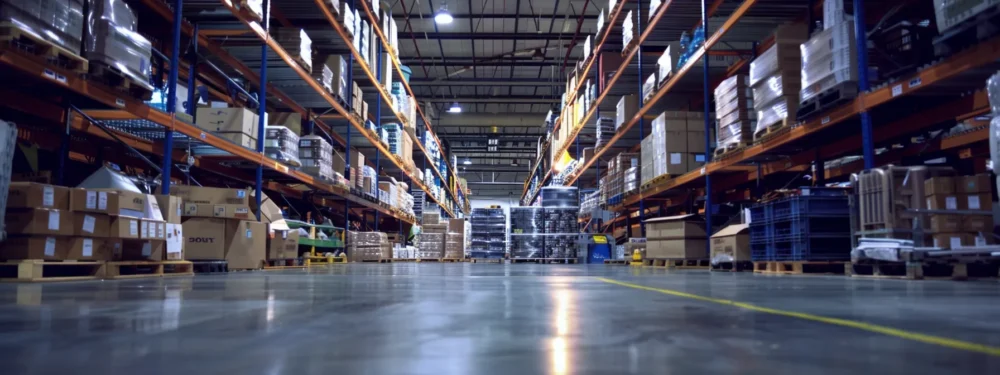
One of the most compelling advantages of adopting a kanban system is the potential for significant inventory reduction. By aligning production closely with demand, companies can avoid the costs associated with excess inventory, such as storage fees, spoilage, and capital tied up in unsold goods.
In addition to tangible inventory costs, kanban minimizes the hidden expenses of inventory mismanagement. Reduced inventory levels mean less time spent on counting, handling, and managing stock, which can lead to indirect savings in labor and operational efficiency.
The cost-effectiveness of kanban further manifests in its impact on reducing waste. Manufacturing entities that align themselves with lean principles through kanban often report lower rates of defects, rework, and overproduction—all aspects that bleed financial and material resources.
Enhancing Visibility and Responsiveness in Supply Chain Operations
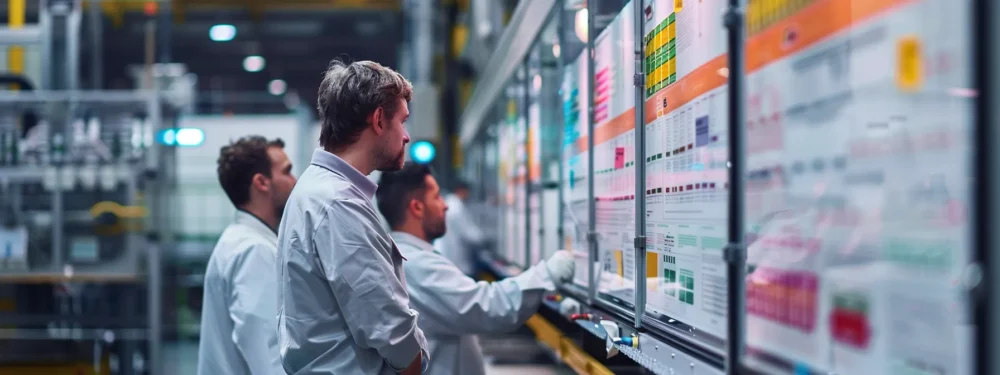
Visibility into operations is crucial for a responsive supply chain, and kanban offers unparalleled transparency. The system provides a comprehensive overview of the state of production and inventory levels, allowing for agile responses to changing market conditions and customer demands.
This heightened visibility is particularly advantageous when dealing with complex supply chains that span multiple locations or involve a plethora of products. Kanban’s universal language of colors, cards, and clear signals facilitates coordination across diverse teams and geographical boundaries.
Implementing Kanban Successfully: Best Practices for Manufacturers
To reap the benefits of kanban, manufacturers must consider several best practices during implementation. It begins with a thorough analysis of existing processes and identifying areas that are prime for kanban’s introduction. Key stakeholders should be engaged from the outset to ensure buy-in and successful adoption of the system.
Training and education are pivotal, as a deep understanding of kanban’s principles among all team members promotes effective execution. This might involve workshops, simulation games, or on-the-job training methods to ensure concepts are understood and embraced.
Overall, the kanban inventory system presents a robust solution for modern manufacturing and supply chain challenges. With its focus on efficiency, agility, and visibility, kanban empowers businesses to stay competitive in a fast-paced market. Adopting kanban principles can lead to improved workflow, reduced costs, and enhanced supply chain responsiveness, providing a strategic advantage that echoes throughout the organization’s operational success.