Managing a DIY shop involves juggling various tasks, but one of the most critical is ensuring the backroom is well-organised and safe. A tidy and hazard-free storage area boosts efficiency and significantly reduces the risk of accidents.
A well-organised backroom is the backbone of any retail operation. It allows for easy access to stock, quick restocking of shelves, and a safer working environment for your employees.
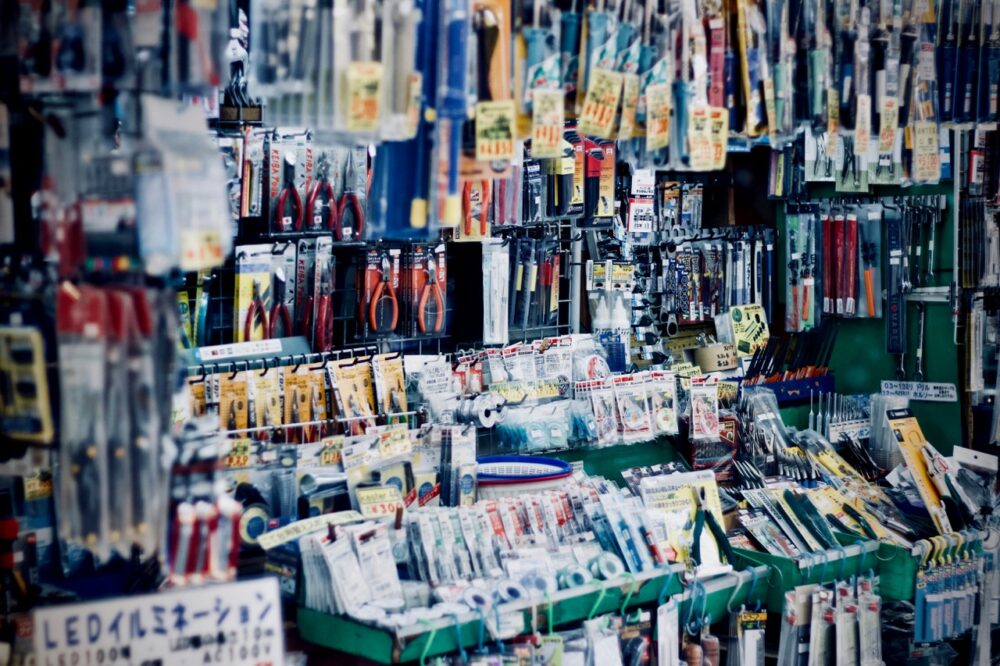
Categorising Inventory
Organising inventory by category is an effective way to maintain order in the backroom. Group similar products together, such as electrical supplies, painting equipment, or gardening tools. This method not only makes it easier to locate items quickly but also helps keep the backroom neat and orderly. Clear organisation saves time and reduces frustration for staff searching for specific products.
Labelling shelves and bins clearly is a simple yet highly effective organisational tool. Use large, easy-to-read labels to identify where each category of items is stored. This practice can significantly cut down the time spent searching for products and improve overall efficiency. Consistent and clear labelling ensures that even new or temporary staff can find what they need without delay.
Implementing a Rotation System
A first-in, first-out (FIFO) system is essential for managing stock effectively, particularly for items with a shelf life. By placing new inventory behind older stock, you ensure that older items are used first. This practice minimises waste and ensures that products are sold before their expiration date. An effective rotation system helps maintain product quality and customer satisfaction.
Train your staff on the FIFO system and remind them regularly to check dates and rotate stock accordingly. Consistent implementation of this system helps maintain order and reduces unnecessary losses. An organised rotation system also means that your backroom remains neat, as products are continually moved and refreshed rather than accumulating dust and becoming disorganised.
Ensuring Safe Storage of Hazardous Materials
Storing hazardous materials requires strict adherence to safety guidelines. Use a hazardous substance cabinet for chemicals and other dangerous items. These cabinets are specifically designed to contain spills and prevent accidents, protecting both your staff and the environment. Ensuring these materials are correctly stored minimises the risk of dangerous incidents.
A COSHH locker is also essential for storing substances that fall under the Control of Substances Hazardous to Health regulations. Proper storage of these materials is not only a legal requirement but also a crucial aspect of workplace safety. Clearly label all hazardous materials and ensure they are securely stored to prevent accidental exposure or spills. Regular checks and maintenance of these storage units will further enhance safety.
Maximising Vertical Space
Utilising vertical space in your backroom is an excellent way to increase storage capacity without compromising floor space. Install sturdy shelving units that reach up to the ceiling, making use of the often-overlooked vertical dimension. This approach not only expands your storage options but also keeps the floor area clear, reducing the likelihood of trips and falls.
Ensure that heavier items are stored on lower shelves while lighter items are placed higher up. This distribution helps maintain the stability of shelving units and prevents them from toppling over. Regular inspections of shelving for signs of damage or wear are essential to maintain safety. Maximising vertical space efficiently helps in keeping the backroom organised and safe.
Keeping an Inventory Management System
Investing in a robust inventory management system is crucial for maintaining accurate stock levels and locations. Digital systems can automate the tracking process, alerting you when stock levels are low or if there are discrepancies. This technology reduces manual errors and streamlines inventory control, making your backroom operations more efficient.
Regularly update the inventory management system with new stock arrivals and sales data. Keeping accurate records ensures you have a real-time view of your inventory, simplifying the process of managing orders and preventing stockouts. An efficient inventory system not only enhances organisation but also supports better financial management by reducing losses and overstocking.
Prioritising Staff Training
Effective training is vital for maintaining a safe and organised backroom. Ensure all staff are well-versed in safety procedures, including how to handle hazardous materials and emergency protocols. Regular training sessions reinforce these practices and keep safety at the forefront of daily operations. Well-trained staff are more likely to follow proper procedures, reducing the risk of accidents.
Encourage staff to report any safety concerns or suggestions for improvement. Creating an open line of communication fosters a proactive approach to safety and organisation. Staff feedback can provide valuable insights into potential hazards or inefficiencies, allowing you to address them promptly. Regularly reviewing and updating training programmes ensures they remain relevant and effective.
Conclusion
A well-organised and safe backroom is crucial for the efficient operation of your DIY shop. By assessing your space, categorising inventory, implementing a rotation system, ensuring safe storage, maximising vertical space, keeping an inventory management system, prioritising staff training, and regularly reviewing practices, you can create a secure and productive environment. These strategies not only protect your staff but also enhance your store’s overall productivity and success.